2016 BYU Baja Vehicle
For the 2015-2016 school year, I was a part of the SAE Baja team at BYU, as one of two engineers assigned to design and build the vehicle's suspension.
CATIA V5 was used extensively to design and analyze the vehicle's various components, and Autodesk VRED and Fusion 360 were used to render possible color schemes.


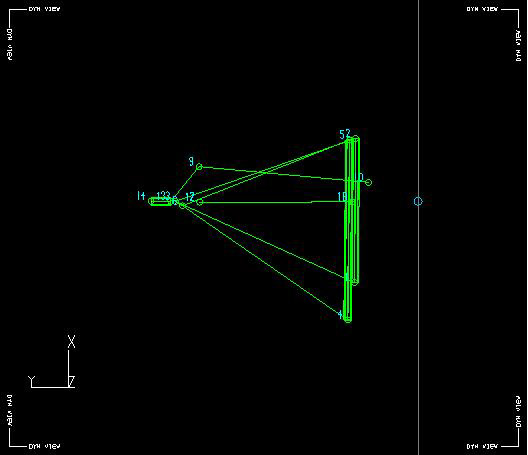
Lotus' Suspension analysis software, SHARK, was used to design, analyze, and improve the static and dynamic behavior of the suspension.
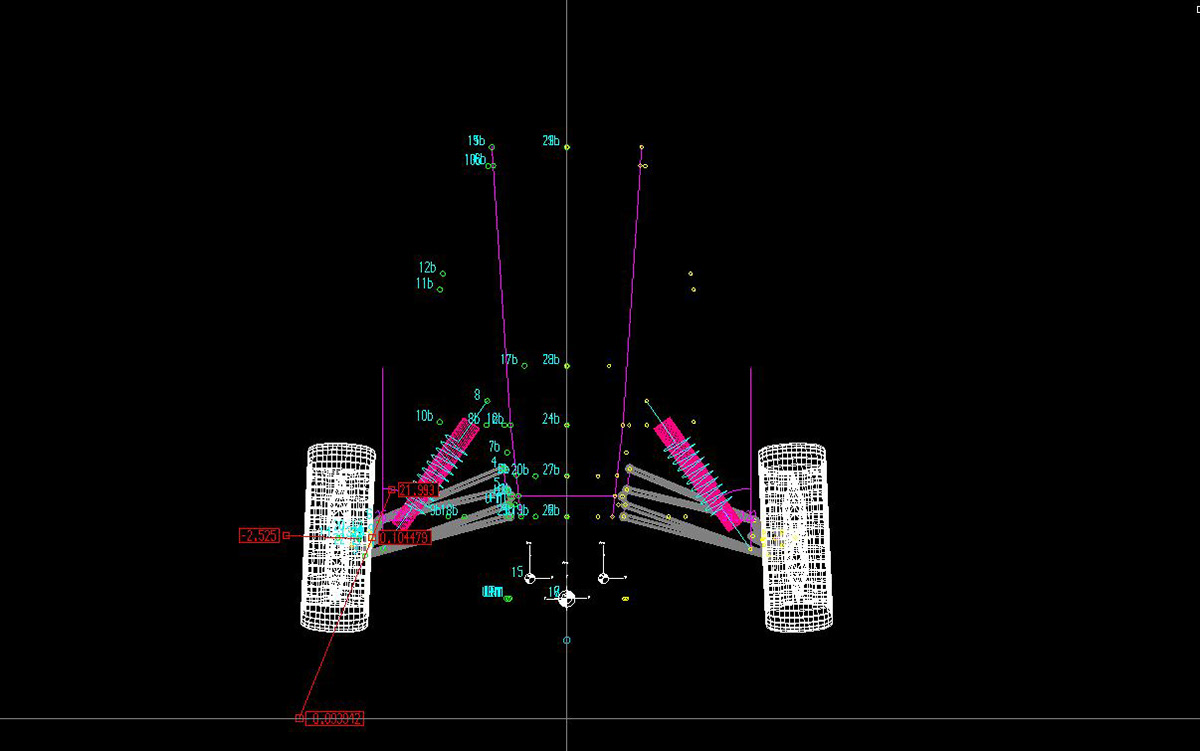
Front Knuckle Design
I introduced this flat-pack style concept and oversaw the development of this design

The front knuckles are constructed from 8 pieces of plate steel, which were cut by water-jet, and a steel tube. This design improved performance, as well as reduced the cost by 85% compared to machining knuckles from a block of 6061 aluminum
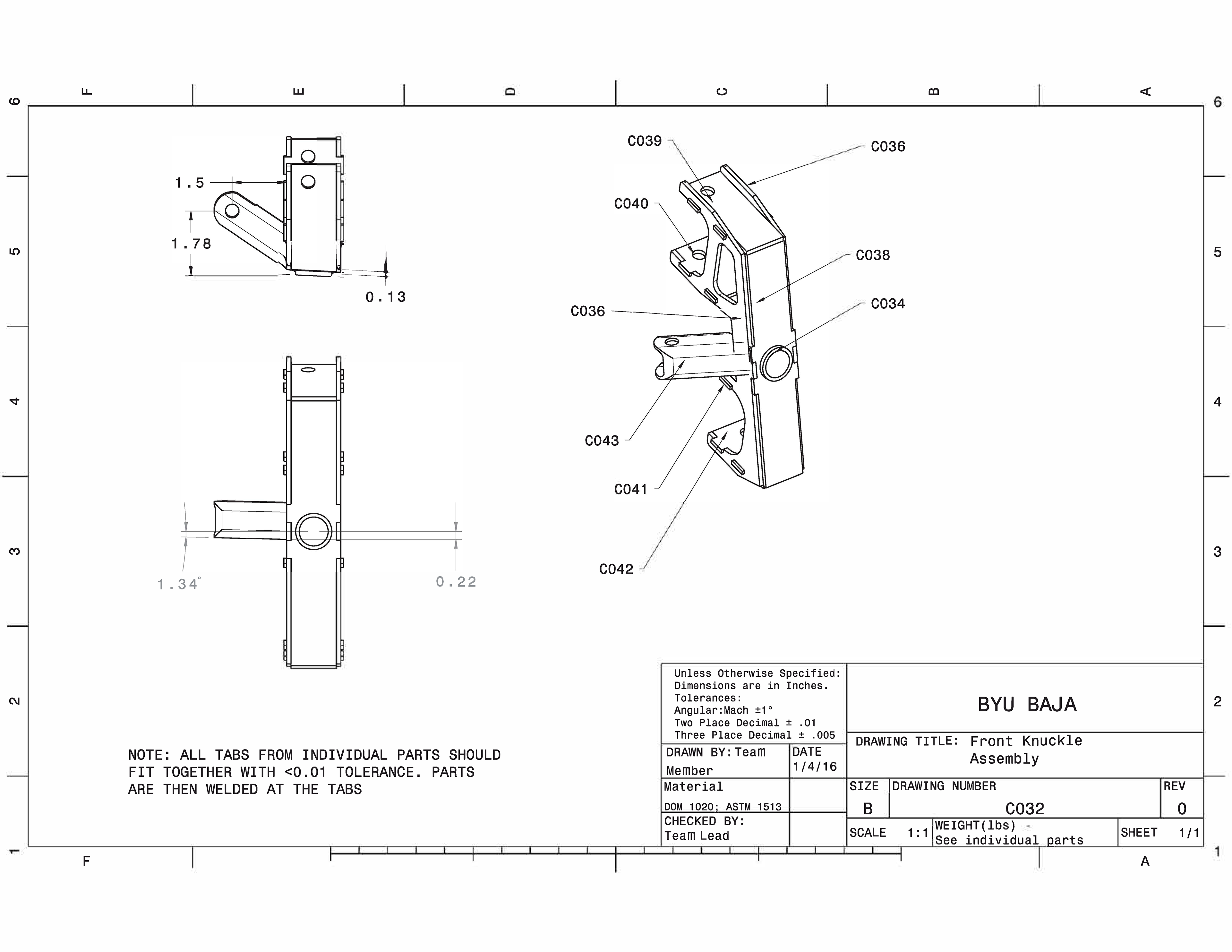
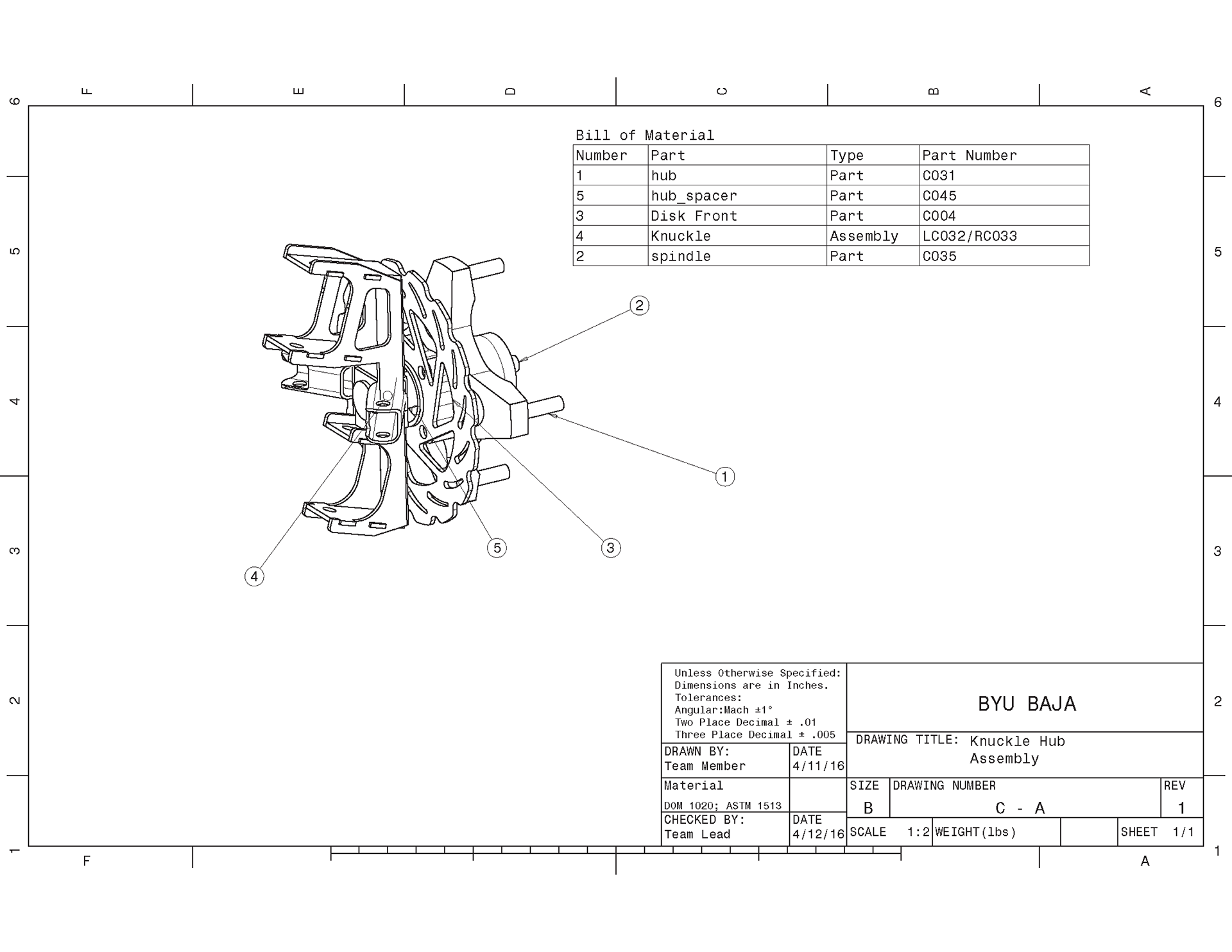
This innovative design allowed for quicker and less expensive prototyping as the suspension and steering were being developed. If any changes to the design were needed, A modified model could be redesigned and fabricated in less than half a day's time.
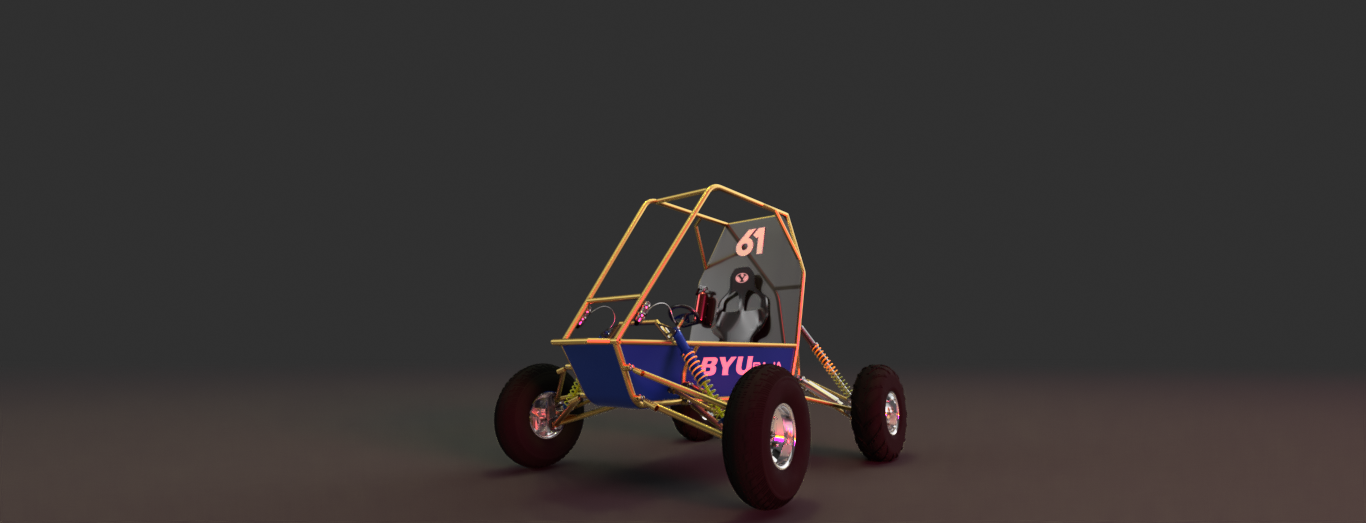
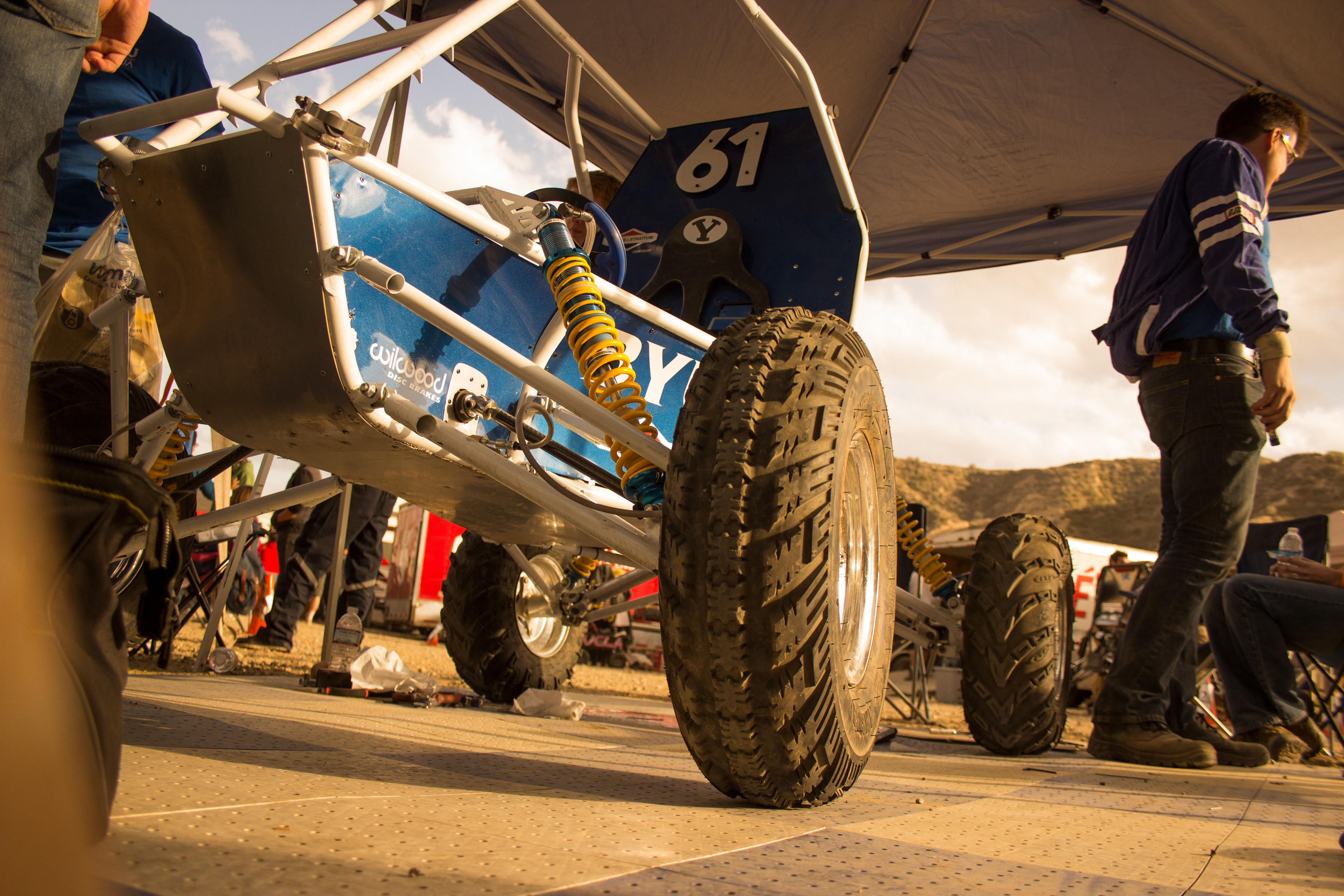